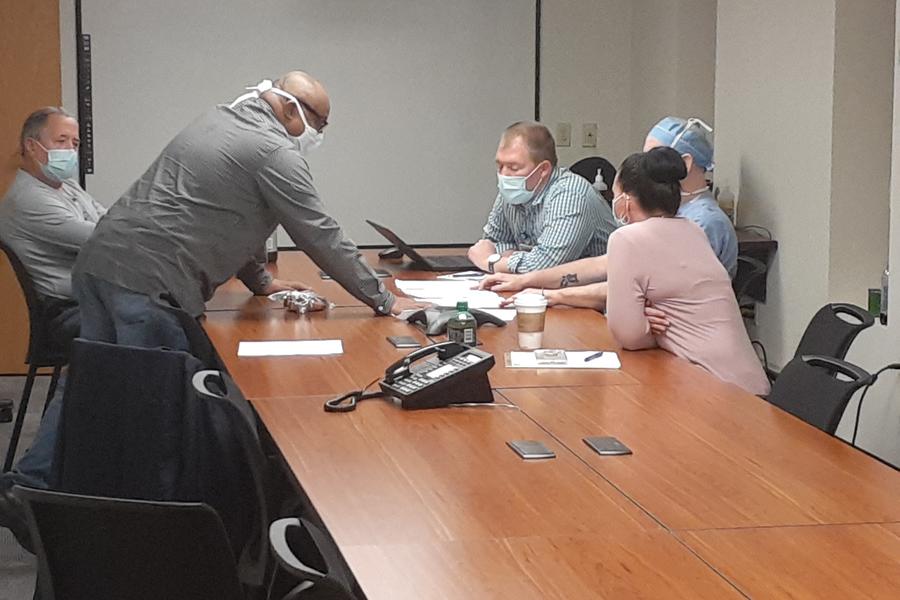
The Coronavirus pandemic has changed many ways we care for patients; manage visitors, vendors and guests; and even run hospitals. CAMC's command center opened in mid-March to provide a coordinated response to COVID-19. It has relied on many experts from various disciplines to support clinical providers. We continue to profile some of those experts who've worked tirelessly behind the scenes to provide information we need to provide the best care for every patient, every day.
The supply chain management department supports the clinical team and delivery of quality patient care through the procurement and distribution of supplies and services. For many years, its motto has been "delivering the right product, at the right time, at the right price."
During the COVID-19 pandemic, the role of supply chain quickly shifted from working in the shadows to being thrust into the spotlight.
"Our team has spent countless hours searching for alternative suppliers and products to ensure the care and safety of our patients and staff," said Steve Perry, associate administrator, supply chain management. "With this, there have been many hurdles and challenges that change daily. Early on, the national demand far outweighed what the national supply chain was prepared to handle. Daily backorders forced the purchasing team to source from non-traditional suppliers, and in some instances, that meant having to pay upfront for supplies. Fortunately, we received all product ordered."
In addition to the challenge of an already overwhelming national supply chain, the Federal Emergency Management Agency was commandeering vendor's supplies and controlling where product could be sent, generally to designated hot spots.
Some health care systems with product sourced direct from overseas had their deliveries seized when reaching customs. The shipping costs soared due to the demand, and getting product scheduled for delivery out of China was taking several weeks longer than usual. One of the unfortunate realities of the PPE medical supply industry that this crisis has highlighted is the unsustainably and high dependence on non-US based manufacturers.
"Due to the global impact of the pandemic, many of these manufacturers were shut down and not producing PPE in any quantities, certainly not sufficient enough to manage the limitless demands this crisis created," Perry said. "Second is the realization that our medical supply manufacturing needs many more U.S.-based suppliers. A national discussion around this subject has begun."
Supply chain immediately began planning when COVID-19 started spreading in the U.S. The data management team developed an inventory projection tool based on increased demand as COVID-19 cases increased. Today, key inventory items are monitored on a daily basis allowing supply chain to communicate with the command center in the event a specific product is in danger of running low or out. In several instances with the clinical teams, changes were implemented to assist in prolonging inventory supply. An online requisition system also was developed that allows designated units to place orders as needed for frequently-used PPE items.
The material handling center team, which has the day-to-day responsibility of managing inventory and receiving daily vendor deliveries, has transitioned from an average of five days on hand to 30-90 days, depending on storage requirements. Daily visits to the COVID-19 units help ensure supply has been maintained and, if necessary, staff have made multiple trips to deliver supply at night and on weekends. Emergency backup carts were created for each COVID-19 unit, plus an additional cart that nursing supervisors have access to after hours.
It has been almost as difficult a task to predict use of supply on the COVID-19 units as it has been to obtain product from suppliers.
"Our linen department quickly went into action and began processing reusable isolation gowns when obtaining disposable gowns became too difficult," Perry said. "The linen team worked many overtime hours. Purchasing contributed by sourcing and helping convert many of our units to the new reusable gown."
The couriers and transportation team have been making increased runs to help move PPE. The print shop produced educational materials and many of the materials about the social distancing seen throughout the hospitals. It even supported the local United Way team with food deliveries throughout the state to families and individuals severely impacted by the economy and job loss we all have experienced.
In the past, the supply chain management team has been on the ground for H1N1, Ebola and the water crisis. However, it has never faced anything quite like this pandemic that has continued for such an extended period of time and put so much strain on both internal and external resources.
"Personally, I am extremely proud of this team's endurance and desire to ensure supply is available for our organization throughout this unprecedented time," Perry said. "I'm grateful to the clinical leadership and front-line clinicians who are caring for patients in such a heroic manner."